What is gas surge?
Gas surge is a rush of gas from a TIG or MIG torch when the trigger is pulled. The initial rush is at several times the required flow rate, before settles down to the value set by the flow meter.
The consequences of gas surge
There are three issues that are caused by gas surge.
- Wasted gas. The surge happens every time the trigger is pulled and if there is a lot of stop-start welding, the amount of gas lost can be high, and that costs money.
- Loss of shielding. The gas flow rate during the surge is several times that required for shielding and that can cause turbulence and draw air into the gas flow. This may result in weld defects such as porosity, and poor weld starts.
- Distraction. Some welders simply find the gas surge annoying.
For an individual welder, none of these issues may be important, but in an industrial setting where there are several welders and standards to be met, they can be significant. Manufacturers of devices to mitigate gas surge routinely claim a 50% saving in shielding gas.
The cause of gas surge
Welding processes that use a shielding gas, such as MIG and TIG generally use:
- A source of shielding gas
- A regulator to reduce the cylinder pressure to a working pressure
- A flow meter to adjust the flow of the shielding gas
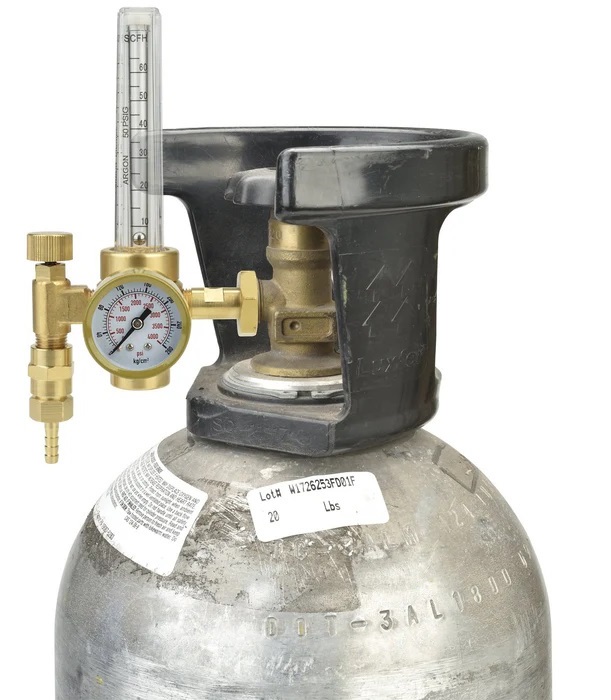
The regulator-flowmeter shown reduces the cylinder pressure (say 2000 psi) to a working pressure of 50 psi for the flow meter. The knob operates a needle valve to adjust the flow which in indicated on the Thorpe Tube flow meter by the floating ball.
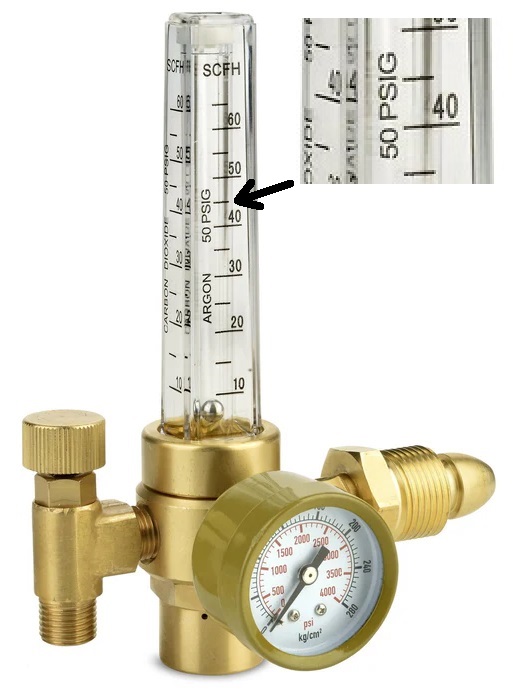
During welding, the shielding gas flows from the flowmeter at the required rate – say 10 L/m or 20 CFH. The gas pressure in the hose between the flowmeter and the torch will be about 4 psi.
When the trigger is released, the gas solenoid in the welding machine stops the gas flow and the pressure in the gas hose between the flowmeter and the gas solenoid increases to 50 psi – the calibration pressure of the flow meter. Depending on the gas hose, it will likely expand because of the increased pressure and so holds more gas.
When the trigger is pulled to resume welding, this pressurised gas contained on the gas hose is released in a sudden rush causing a gas surge.
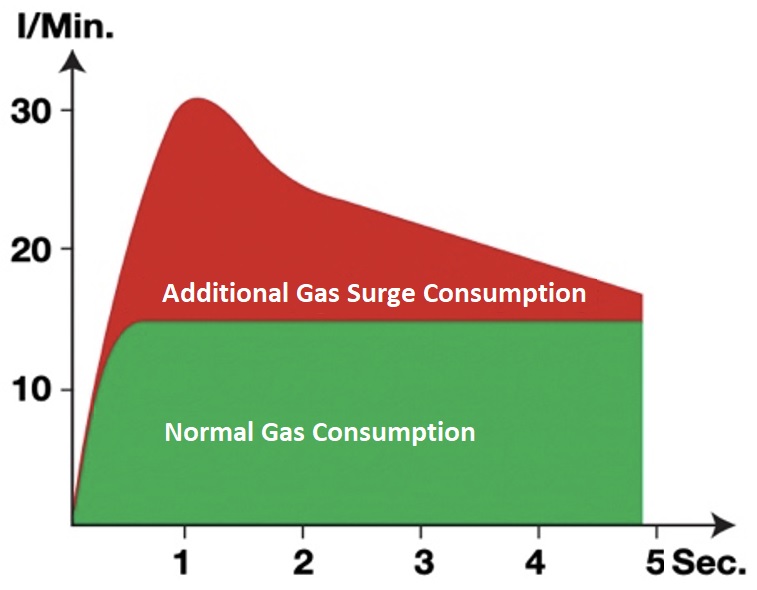
Reducing gas surge
Gas surge is caused by the volume and pressure of the gas stored in the gas hose between the flowmeter and the gas solenoid when the trigger is off. Clearly then, gas surge can be reduced if the volume or pressure, or both, can be reduced.
Volume
The volume of the hose is reduced by:
- Using only the length of hose that is needed,
- Using only the inside diameter that is required for proper gas flow and
- Using a gas hose that does not expand significantly with pressure
Pressure
Pressure directly affects the volume of gas within a container. Using the ideal gas law, the relationship between volumes of gas at different pressures can be determined.
VOUT = VIN * (pIN/pOUT)
Where:
VIN = Volume in the hose
pIN = Pressure in the hose
VOUT = Volume of gas at the outlet
pOUT = Pressure at the outlet
The pressure in the hose is 50 psi (using the example above) and the pressure at the outlet is 4 psi so:
VOUT = 12.5 * VIN
If the calibration pressure of the flowmeter could be halved, expansion of the gas would be halved and so would the gas surge.
Summary
Gas surge can be reduced by minimising the volume of the gas hose (shorter, smaller ID and more rigid) and by using a flowmeter with a lower calibration pressure – say 20 or 25 psi.
Note that some would simply reduce the preset pressure of any flowmeter. That will reduce gas surge, but the flowmeter will no longer be calibrated. In the real world, that might not matter to you.
Commercial gas surge mitigation solutions
Most manufacturers use either the volume and pressure approach as outlines above, or they use a calibrated orifice which simply limits the maximum flow to something deemed reasonable.
Commercial Examples
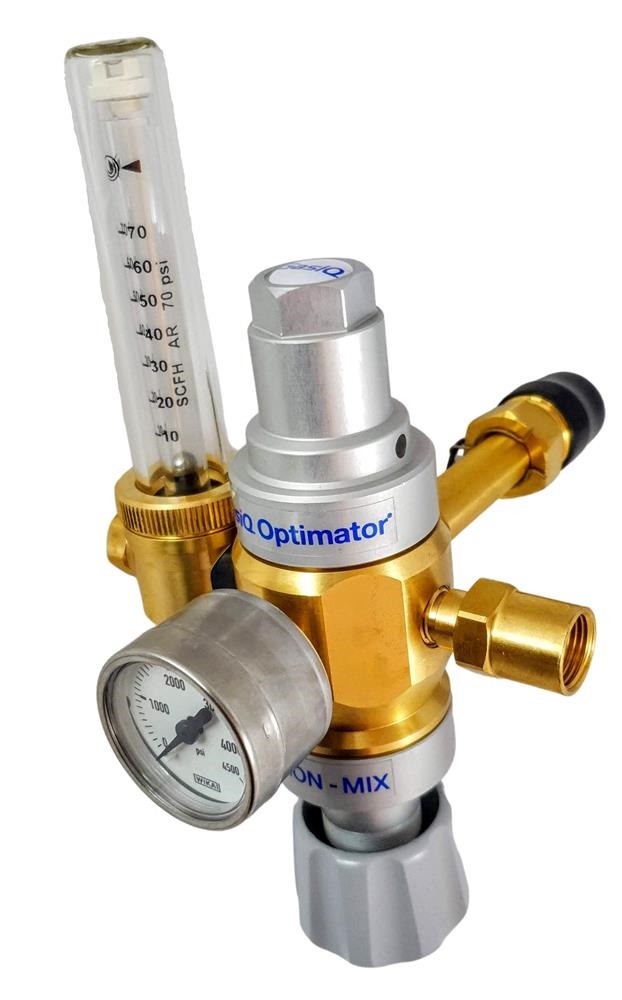
The GasIQ Optimator® is a high performance dual stage regulator with an in-built economizer and meter to gauge flow. It is mainly used for advanced gas shielded welding production applications, where it will reduce the total welding cost by decreasing the gas consumption by up to 50%. In addition, reduced porosity sensitivity improves weld quality.
Tests have shown that Volvo saves at least 43% gas through the installation of Optimator®.
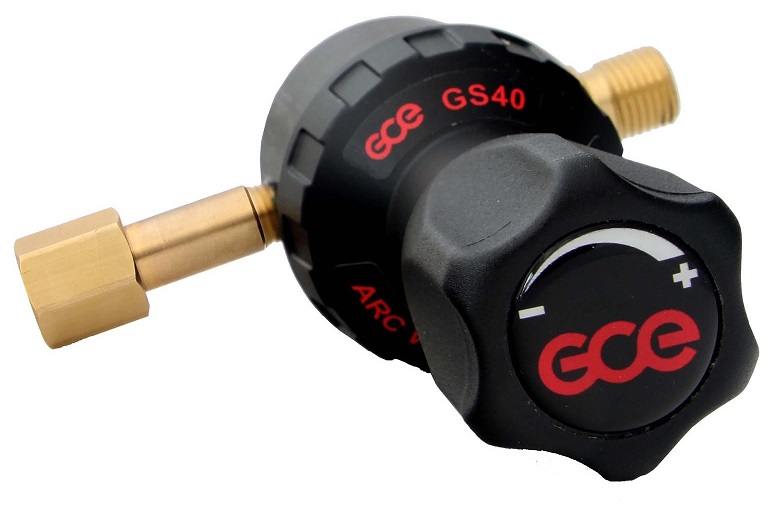
GCE GS40.
Cost of the shielding gas is important factor influencing total cost balance of the welding operation. The savings with GS40 represents up to 0,5ltr of the shielding gas on each average weld. Optimal gas delivery with proper defined pressure and flow-rate improves quality of welding. Cost saving and quality improvement in this area give the advantage to the user on the competitive market.
HOW DOES IT WORK?
When you close the gas flow at common pressure regulator during the welding process interruption, the outlet pressure in the connecting hose rises up much above the optimal level (acc. to ISO 2503 up to 30%). Then the volume of the gas, higher than really needed, is blowing through the system after the welding process starts again by switching on the arc on the welding torch. GS40 minimises amount of such waste gas cumulated in the connecting hose. The optimal, predefined gas flow is delivered to the welding process during all its phases. Adjustable variant with the handwheel (GS40A) is to be used with regulators with flow-meter, fixed variant (GS40F) with regulators with litre-scaled pressure gauge.

Harris Inert Gas Guards are designed to save shielding gases by reducing the gas surge when a MIG gun or TIG torch is activated. Because they are designed to reduce the pressure held in supply hose, gas waste is reduced when the gun or torch is triggered. They save shielding gases also by delivering a controlled flow rate. Operators will typically set shielding gas flow rates higher than necessary for a welding operation. Once set by a supervisor, the Inert Gas Guard delivers the precise amount of flow for the operation, eliminating the needless waste of gas.
https://www.harrisproductsgroup.com/en/Products/Equipment/Pressure-Regulation/Inert-Gas-Guards