Arc welding is a form of fusion welding where the heat needed to fuse the metal is created by an electric arc contained in a plasma of positive and negatively charged particles. The polarity of the voltage that sustains the arc has a significant effect on:
- Arc stability
- The amount of spatter generated
- Depth of fusion and joint penetration
- Weld (arc) width
- Deposition rate
- Cleaning action
- Heat, distortion and residual stress
Polarity is determined by the design of the power source (welding machine) and the way the electrode holder (torch) and return lead (work lead) are connected to it.
A welding machine may be direct current (DC) where the current flows in one direction only, or alternating current (AC) where the current periodically changes direction. At one time, the AC welding current changed directions at the same rate (called frequency) as the supply voltage, that is, 50Hz. Modern AC welding machines allow the frequency of the welding current to be set.
When the torch is connected to the negative terminal of a DC welding machine and the return lead is connected to the positive terminal, the polarity is known as DC-electrode negative or DCEN.
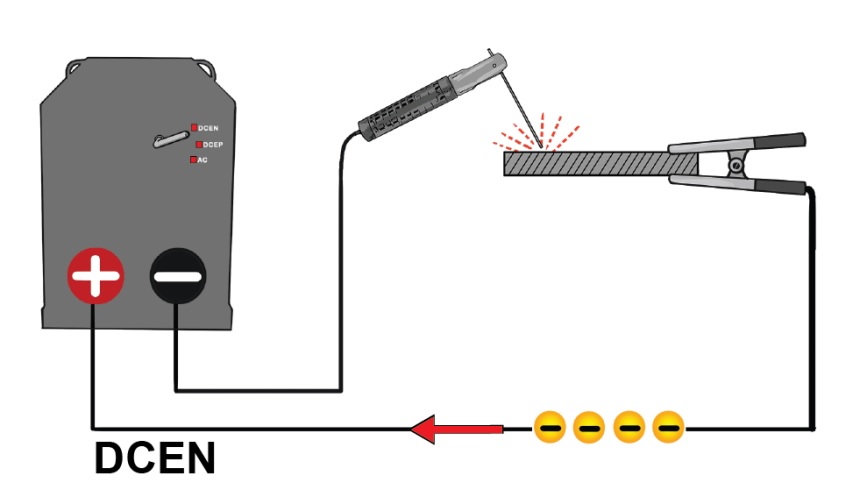
When the torch is connected to the positive terminal of a DC welding machine and the return lead is connected to the negative terminal, the polarity is known as DC-electrode positive or DCEP.
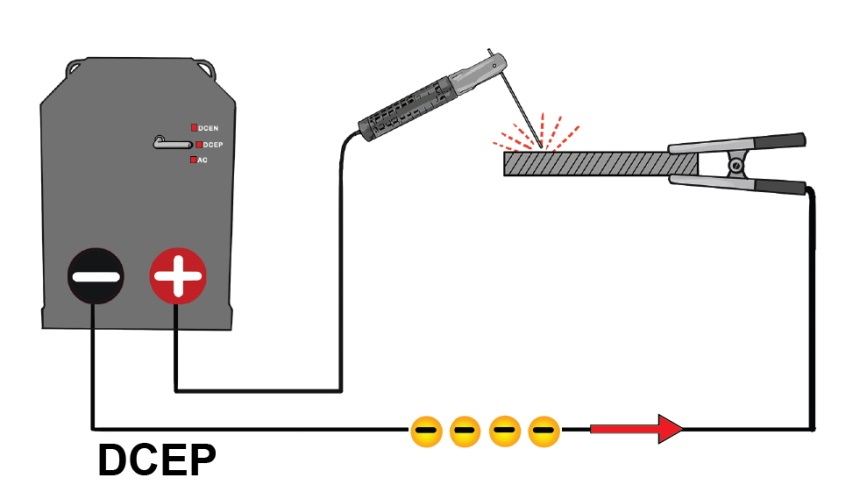
DCEN and DCEP were once known as “straight polarity” and “reverse polarity” respectively and those terms will be found in older reference books.
Polarity of the Arc
Although the plasma in the arc is composed of both negatively charged electrons and positively charged ions, there are many more electrons than ions, so the bulk of the arc current consists of the movement of electrons moving from the cathode (negative side) to the anode (positive side).
DCEN
In DCEN, electrons are emitted from the electrode and imparted with a significant amount of energy (the work function) and gain additional kinetic energy being accelerated to very high speeds while traveling through the arc. These high-energy electrons collide with the workpiece, giving up their energy and generating considerable heat in the workpiece.
About two-thirds of the net heat available from the arc (after losses from sources including radiation and ion movement) enters the workpiece.
Note that other factors can alter this heat distribution and good use can be made of this as will be described later.
As a consequence, DCEN results in deep penetrating, narrow welds and higher workpiece heat input. High heat input to the workpiece may or may not be desirable, depending on factors such as the required weld penetration, required weld width, and concern for distortion or residual stress.
DCEP
In DCEP, the electrode is connected to the positive terminal of the welding machine. The heating effect of electrons is now at the electrode rather than at the workpiece so a shallow weld is produced. Furthermore, a large electrode must be used in order to prevent the electrode tip from melting. The positive ions of the shielding gas bombard the workpiece helping to break off the oxide film and produce a clean weld surface. Therefore, DCEP can be used for welding oxide-forming materials such as aluminium and magnesium.
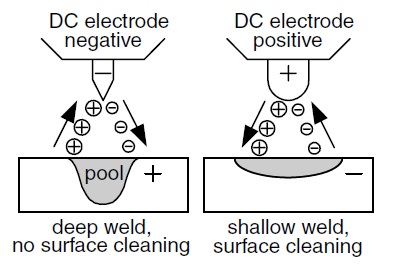
Gas Tungsten Arc Welding (GTAW)
GTAW of steels uses DCEN, a shielding gas and a non-consumable tungsten electrode. Two-thirds of the net heat available from the arc fuses the workpiece causing deep penetration and coalescence to complete the weld.
In the case of oxide-forming materials such as aluminium and magnesium, DCEN for penetration and DCEP for its cleaning action can be used together. This is referred to as Alternating Current (AC) welding.
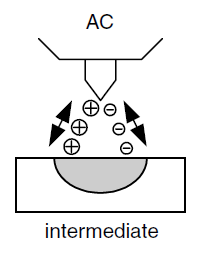
With AC, the electrode is connected to the negative terminal of the welding machine. Even though the welding current is AC, the correct “polarity” is required so that the balance control operates correctly.
The heating effect of electrons during the EN cycle gives penetration at the workpiece while the EP cycle cleans it.
The precise mechanism of the cleaning action is debated but is likely a combination of:
- The positive ions of the shielding gas bombarding the workpiece helping to break off the oxide film
- The emitted electrons from the metal being drawn through the oxide layer by the electric field across it causing a breakdown of the oxide layer.
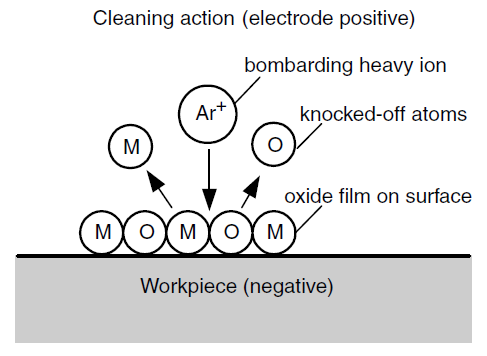
Originally, AC GTAW used a balanced sinusoidal EP-EN current at the mains frequency (50Hz).
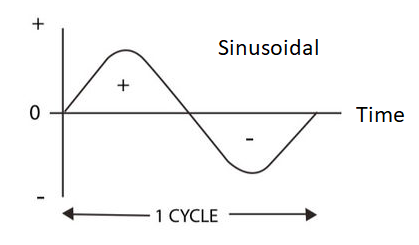
Although this has the desired result of cleaning and penetration, the arc is unstable. One reason for the arc instability is the slow zero crossing of the sinewave leading to the arc being extinguished for a short period. The other reason is that the positive (cleaning) cycle is more difficult to restart leading to arc rectification.
Because of this arc instability, continuous HF Stabilisation is used to maintain the arc. HF can also be used to start the arc when the torch trigger is pulled.
Another method of reducing arc instability at the zero crossings is to use a square wave rather than a sine wave. A square wave switches from EP to EN and back much faster than a sine wave so the arc is less likely to be extinguished at the zero crossings. Continuous HF is not generally required when using a square wave welding current.
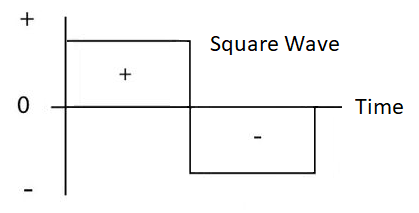
Further advances in technology permitted first, the ratio of EP to EN times to be selected, and later, the ratio of EP to EN currents (or voltages) to be selected.
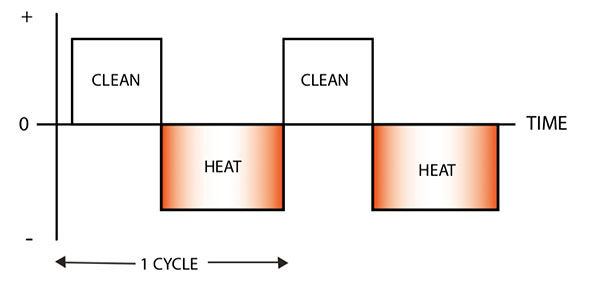
Generally, less time is needed for cleaning than for penetration and, in practice, only as much cleaning is used as is necessary for the task as hand as increasing cleaning reduces penetration.
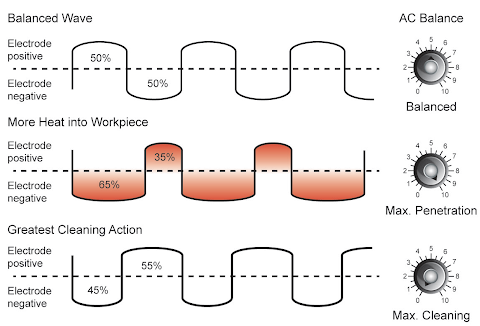
Gas Metal Arc Welding (GMAW) & Fluxcore Arc Welding (FCAW)
GMAW and FCAW-G
GMAW and FCAW-G generally use DCEP, a shielding gas and a consumable electrode.
In addition, FCAW-G uses a cored wire filled with a “flux” consisting of metal fillers such as iron powder, alloying elements to modify the metallurgy of the weld metal and deoxidisers to help remove contaminants.
Two-thirds of the net heat available from the arc is directed at the anode, which in this case, is the consumable electrode. The electrode melts and the molten droplets are propelled by electro-magnetic pinch effect to impact the workpiece. This transfer of heat back to the workpiece is what allows GMAW and FCAW-G to achieve good penetration and cleaning using DCEP.
FCAW-S
FCAW-S generally uses DCEN and a consumable electrode.
In addition, FCAW-S contains chemicals in its flux to create a shielding gas – generally carbon dioxide.
Why is this different from FCAW-G? Unlike FCAW-G, FCAW-S does not use a shielding gas to protect the wire electrode between the contact tip and the arc. Without that protection, Nitrogen (N2) and Oxygen (O2) in the atmosphere would react with the hot wire before it melted into the puddle and could be protected by the self-shielding gas.
N2 and O2 gases in the vicinity of the wire exist as negative ions (eg N3- and O2-) and one way to keep them away from the wire is to make the wire negatively charged. This is achieved by using DCEN.
There remains, of course, the need to stabilise the arc and effect the required heat transfer. This is achieved by chemicals added to the flux – in the same way as is done in SMAW fluxes.
Shielded Metal Arc Welding (SMAW)
SMAW generally uses DCEP and a consumable, flux covered, electrode.
The flux contains chemicals to create a shielding gas – generally carbon dioxide – in addition to metal fillers such as iron powder, alloying elements to modify the metallurgy of the weld metal and deoxidisers to help remove contaminants.
Unlike FCAW-S, the flux on the outside of the electrode protects it from the atmosphere so there is no need to reverse the polarity.
SMAW differs from GMAW and FCAW-G in that penetration and arc stability are determined more by the flux used than the polarity used.
Summary
Polarity has a significant role to play in determining the properties of a weld.
Manufacturers specify the polarity and other parameters needed to obtain the claimed metallurgical properties of the filler and there may be procedures that must be followed.
Nevertheless, understanding the physics involved will help to make informed decisions about welding polarity and other parameters.
Image Sources
- Mast Image: https://unsplash.com/@atieh_khoshraftar
- AC Welding images: Welding Metallurgy, 2nd Edition – Sindo Kou, page 14
- AC Welding Images: The GTAW (TIG) Process (TIG Handbook)
- AC Welding Images: https://www.jasic.co.uk/differences-between-tig-dc-and-ac
- Balance Image: https://www.cwbgroup.org/association/how-it-works/welding-aluminum-story-aluminum-part-4